










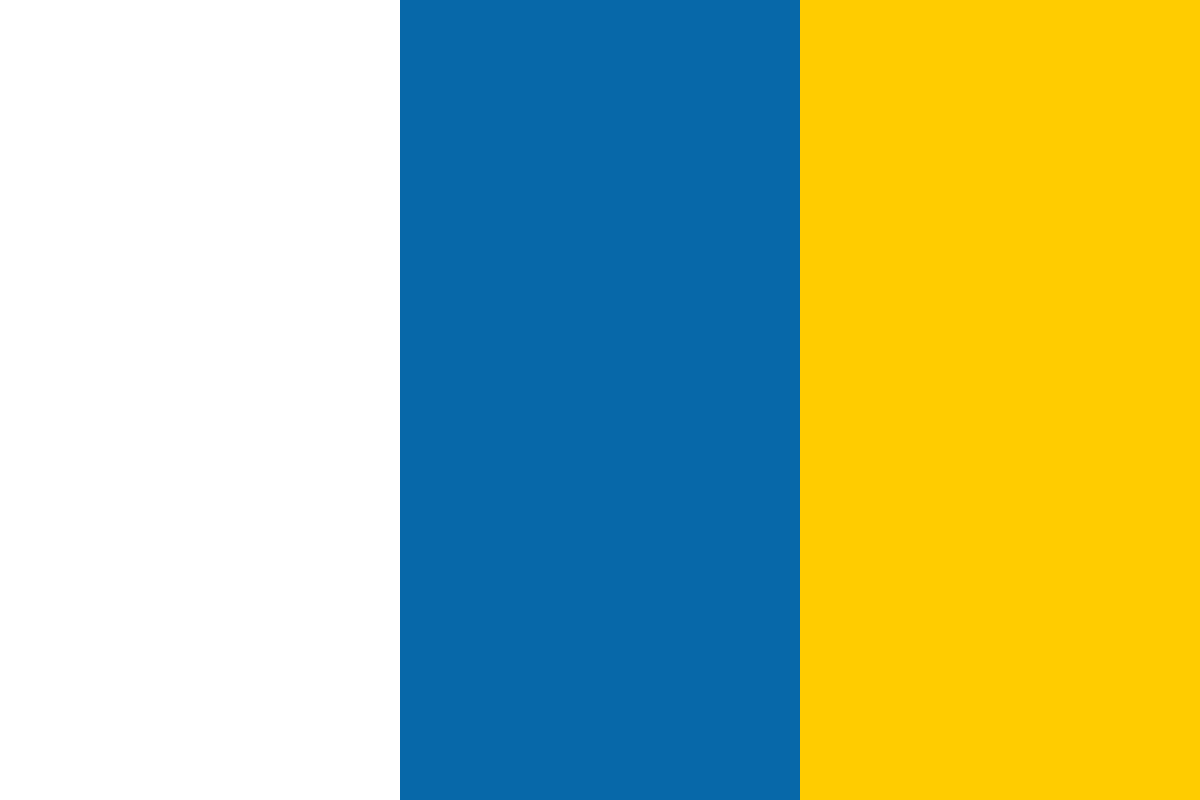

































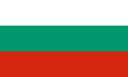








(For more resources related to this topic, see here.)
Manufacturing orders define the product you wish to build and the resources that are required to build it. They also designate when you wish to produce the product.
When it is time to actually produce the product, you then inform OpenERP of each of the products produced, and your manufacturing order changes to a status of Complete . In a typical workflow, your raw materials are moved out of the inventory and your finished product is added into your inventory.
After a product has been produced and has been put into the inventory, it can be packaged and delivered to the customer. Depending on the specific manufacturing environment, a product may not even sit in a physical inventory location at all, and instead may be shipped almost immediately to the customer. Meanwhile in another industry, you may have a product that is produced and then sits in a warehouse for months before delivery. Of course, it is always possible that something gets produced and gets left in dead stock. In this case, you would never have a delivery order and instead use a process to determine how to report that dead inventory.
Much like configuring the CRM application, often the most complex part of setting up a purchasing and manufacturing system is not the ERP software itself. Instead, the real challenge is understanding the business requirements and how current processes can best be implemented. If you have never set up a purchasing and manufacturing system before, it is highly recommended that you supplement your knowledge with additional reading on the subject.
In OpenERP you manufacture products by creating manufacturing orders. For our example, we will be printing t-shirts that have a custom-designed logo. The basic manufacturing process itself involves using a screen to apply ink to each of the t-shirts. For now, we don't need to know all the details of this process to begin using OpenERP to help schedule and track the manufacturing of the product.
The basic steps in the process are simple:
We must now install the MRP application so that we can begin configuring our t-shirt production. By now, you should begin to understand the modular nature of OpenERP. Install the MRP application just like you did with the other OpenERP applications. Navigate to Settings | Apps .
The flexibility of OpenERP provides a variety of approaches you can take in setting up your system. Manufacturing can also become a complex topic and is one of the more challenging aspects of setting up any ERP system. For our first manufacturing order, we will ignore many of the advanced options.
Keep it simple at first. There are many options and it will take time to understand them all. If you are new to manufacturing systems, it will take you longer to implement OpenERP, and you should consider hiring professional consultants to assist you.
To create your first manufacturing order, go to the Manufacturing menu, choose Manufacturing Orders , and then click on Create .
This is the manufacturing order as it appears just after you click on Create . The MO in the sequential order number that will be assigned stands for, you guessed it, Manufacturing Order . We will use this form to define our manufacturing order to print our custom-designed t-shirts.
Selecting the product
The only product we have entered into OpenERP so far is a blank Medium White T-Shirt . This t-shirt is currently a raw material. Now we want to produce a new product. We must define what our final product will be after the t-shirt has been printed. For our example, it will be Class of 2013 T-Shirt .
OpenERP allows you to create this product on the fly. Just click on the pop up and choose Create and Edit .
The Product and Procurements tabs should look familiar by now. The most important aspect for this product is the supply method. It is set to Manufacture . Only the products that have the supply method of Manufacture can be selected as a product on a manufacture order.
You will also notice that the Can be Purchased checkbox is unchecked. This will keep this product from appearing in the product list on a purchase order. We have also put on a Manufacturing Lead Time of 3.000 days. This will then impact the dates that are automatically assigned when we create a manufacturing order.