










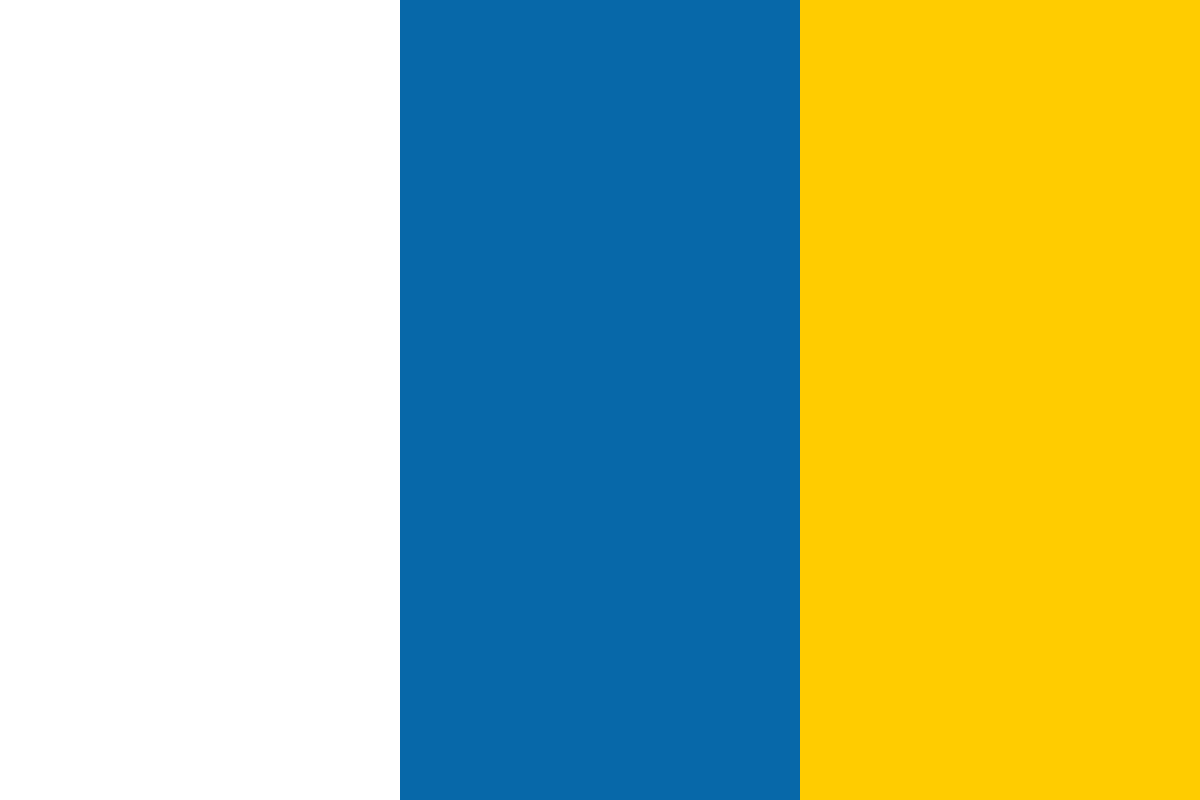

































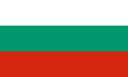








If you’ve visited any social media outlets, you’ve probably come across a never-ending list of new words and terms—the Internet of Things, technological dissonance, STEM, open source, tinkerer, maker culture, constructivism, DIY, fabrication, rapid-prototyping, techshop, makerspace, 3D printers, Raspberry Pi, wearables, and more. These terms are typically used to describe a Maker, or they have something to do with Maker culture. Follow along to learn about my particular journey into the Maker culture, specifically in the 3D printing space.
Maker culture is on the rise. This is a culture that thrives at the intersection of technology and innovation at the informal, social, and peer-led level. The interactions of skilled people driven to share their knowledge with others, develop new pathways, and create solutions for current problems have built a new community.
I am proud to say that I am a Maker-Tinkerer (or that I have some form of motivated ADHD that drives me to engage in engineering-oriented pursuits). My journey started at ground zero while studying 3D design and development.
I knew there was more that I could do with my knowledge of rendering the three-dimensional surface of an object. Early on, however, I only thought about extending my knowledge for entertainment purposes, such as video games. I didn’t understand the power of having this knowledge and the way it could help create real-world solutions. Then, I came across an issue of Make Magazine and it changed my mental state overnight—I had to create tangible things.
Now that I had the information to send me in the right direction, I needed an outlet. An industry friend mentioned a local Hackerspace, known as Deezmaker, which was holding informational workshops about 3D printing. So, I signed up for an introductory class. I had no clue what I was getting myself into as I crossed that first threshold, but by that evening, I was versed in topics that I thought were far from my mental capabilities. I was hooked.
The workshop consisted of part lecture, and part hands-on material. I learned that you couldn't just start using a 3D printer. You actually need to have some basic understanding of the manufacturing process, like understanding that layers of material need to be successfully laid down in order to move on to the next stage in the process. Being the curious, impatient, and overly enthusiastic man-child that I am, this was the most difficult part for me, as I couldn’t wait to engage in this new world.
Almost two years later, I am fully immersed in the world of 3D printing. I currently have a 3D printer at home (which is almost obsolete, by today’s standards) and I have access to multiple printers at a local techshop/makerspace known as Makerplace here in San Diego, Ca.
I use this technology regularly, since I have changed directions in my career as a 3D artist towards Manufacturing Engineering and Rapid Prototyping. I am currently attending a Machine Technology/Engineering program at San Diego City College; (for more info on the best Machining program in the country visit http://www.JCbollinger.com).
The benefit for me using 3D printers is rapidly producing iterations of prototypes for my clientele, since most people feel more reassured in the process if they have tangible and solid objects and are more likely to trust you as a designer. I feel that having access to this also helps me complete more jobs successfully given that turnaround times for updates can be as little as a few hours, rather than days or weeks (depending on the size/scale).
Currently I have a few reoccurring clients that want updates often, and by showing them my progress, the iterations are fewer and I can move onto the next project with no hesitation given how we can successfully see design updates rapidly and minimize the flaws and failures. I produce prototypes for all industries: toys, robotics, vehicles, and so on. Think of it as producing solutions, and how you can either make something better or simpler. Entertaining the idea of a challenge and solving these challenges has benefits as with each new design job you have all these tangible objects to look at and examine.
As a hobbyist, the technology has made it easy to produce new or even obsolete items. For example, I love Transformers, but you know how plastic does two things very well: it breaks and gets lost. I came across a forum where guys were distributing the programs for the arm extrusions that break (no one likes gluing), so I printed the parts that had been missing for decades, rebuilt the armature that had for so long been displaced, and then like magic I felt like I was six years old again with a perfectly working Transformer.
Here are a few things that I've learned along the way:
The FDM process can be done with a multitude of materials; the two most popular options at this time are PLA (Polylactic acid) and ABS (Acrylonitrile butadiene styrene). Both PLA and ABS have pros and cons, depending upon your model structure. The future use of the print and client requests and understanding the fundamental differences between the two can help you determine your choice of one over the other, or in case of owning a printer with two extruders, how they can be combined. In some cases, PVA (Polyvinyl Acetate) is also used as support material (in the case of two extruders) unlike PLA or ABS, which if used as support material will require cleanup when finishing a print. PVA is water soluble, so you can soak your print in warm water and the support structures will dissolve away.
PLA (Polylactic Acid) is a strong biodegradable plastic that is derived from renewable resources: cornstarch and sugarcane. It is more resistant to UV rays than ABS (so you will not see fading with your prints). Also, it sticks better than any other material to the surface of your hotplate (minimal warping), which is a huge advantage. It prints at -180* C, and it can create an ooze, and if your nozzle is loaded it will drip, which also means that leaving a print in your car on a hot day may cause damage.
ABS (Acrylonitrile butadiene styrene) is stronger than PLA, but is non-biodegradable; it is a synthetic monomer produced from propylene and ammonia. This means it has more rigidity than PLA, but is also more flexible. It is a colorfast material (which means it will hold its color for years). It prints at -220*C, and is amorphous and therefore has no true melting point, so a heated bed is needed as warping can and will occur (usually because the bed is not hot enough—at least 80*C —or the Z axis is not calibrated correctly).
For the hobbyist maker, there are a few 3D printer options to consider. Depending upon your skill level, your needs, budget and commitments, there is a printer out there for you.
The least expensive, smallest, and most straightforward printer available on the market is Printrbot Simple Maker’s 3D Printer. Retailing at $349.99, this printer comes in a kit that includes the bare necessities you need to get started. It is capable of printing a 4” cube. You can also purchase it already assembled for a little extra. The kit and PLA filament are available at www.makershed.com.
The 3D printer I started on, personally own, and recommend is the Afina H480 3D printer. Retailing at $1299.99, this printer provides the easiest setup right out of the box, it’s fully assembled, comes with a heated platform for the aid of adhesion and for less chance of warping, and can print up to a 5” cube. It also comes loaded with its own native 3D software, where you can manipulate your .STL files. It has an automated utility to calibrate the printer’s build platform with the printhead, and also automatically generates any support setup material and the “raft”, which is the base support for your prints. There is so much more to it, but as I said I recommend this for beginners, and it is also available through www.makershed.com.
For the person who wants to print, and is at the hobbyist and semi-professional level, consider the next generation in 3D printing, the MAKERBOT Replicator. It is quick and efficient. Retailing at $2899.00, this machine has an extremely high layer resolution, LCD display, and if you run out of filament (ABS/PLA), there is no need to start over; this machine will alert you via computer or smartphone that a replacement is needed.
There are many types of 3D printers available, with options including open source, open hardware, filament types, delta style mechanics, single/double extruders, and the list goes on. My main suggestion is to try before you buy, either at a local hackerspace or a local Makerfaire. It’s a worthwhile investment that pays for itself.
Before you begin, it's also important to choose your design tools. There are many great open source tools to choose from. Here are some of my favorites.
When it comes to design tools, there is a multitude of cost effective and free tools out there to get you started. First off, the 3D printing process has a required “tool-chain” that must be followed in order to complete the process, roughly broken down into three parts:
Here are my best picks for each category, known as FLOSS (free/libre/open source software).
FLOSS CAD tools, for example OpenSCAD, FreeCAD, and HeeksCAD for the most part create these parametric files that usually represent parts or assemblies in terms of CSG (Constructive Solid Geometry) which basically represent a tree of Boolean operations performed on primitive shapes such as cubes, spheres, cylinders, and pyramids. These are modified numerically and with great precision and the geometry is a mathematical representation of such, no matter how much you zoom in or out.
Another category of CAD tool that represents the parts as 3D polygon mesh is for the most part used for special effects in movies or video games (CG). They are also a little more user friendly, and examples would be Autodesk Maya and Autodesk 3ds Max (these choices are subscription/retail-based).
But there are also open source and free versions of this tool such as Autodesk 123D, Google Sketchup, and Blender; I suggest the latter options, since they are free, user friendly, and they are much easier to learn since their options are narrowed down strictly to producing 3D meshes. If you need more precision you should look at OpenSCAD (my favorite), as it was created directly for making physical objects rather than game design or animation. OpenSCAD is easy to learn, with a simple interface, it is powerful and cross-platform, and there are many examples you can use along with strong community support.
Next, you’ll need to convert your 3D masterpiece (.stl) into a machine friendly format known as G-Code. This process is also known as “slicing”. You’re going to need some CAM software to produce the “tool paths,” which is the next stop in the tool chain. Most of the slicing software available is open source. Some examples are Slic3r (the most popular, with an ease of use recommended for beginners), Skeinforge (dated, but still one of the best), Cura, and MatterSlice. There is also great closed source slicing software out there. One in particular is KISSlicer, which is a pro version that supports multi-extruder printing.
The next stop after slicing is using software known as:
This software is usually directly linked to an EMC (Electronic Machine Controller), which controls the printer directly. It can also be linked to an integrated hardware interface that has a G-Code interpreter built in, which loads the G-Code directly from a memory card (SD card/USB).
The last stop is the firmware, which controls the electronics onboard the printer. For the most part, the CPUs that control these machines are simple microcontrollers that are usually Arduino-based, and they are compiled using the Arduino IDE.
This process may sound time consuming, but once you go through the tool chain process a few times, it becomes second nature, just like driving a manual transmission in a car.
When I finished my first hackerspace workshop, I had been assimilated into a culture that I was not only benefiting from personally, but a culture that I could share my knowledge with and contribute to. I have received far more in my journey as a maker than any previous endeavor.
To anyone who is curious, and mechanically inclined (or not), who believes they have an answer to a solution, I challenge you. I challenge you to make the leap into this culture—join a hackerspace, attend a makerfaire, and enrich your life and the lives of others.
Travis Ripley is a designer/developer. He enjoys developing products with composites, woods, steel, and aluminum, and has been immersed in the Maker community for over two years. He also teaches game development at the University of California, Los Angeles. He can be found @travezripley.