










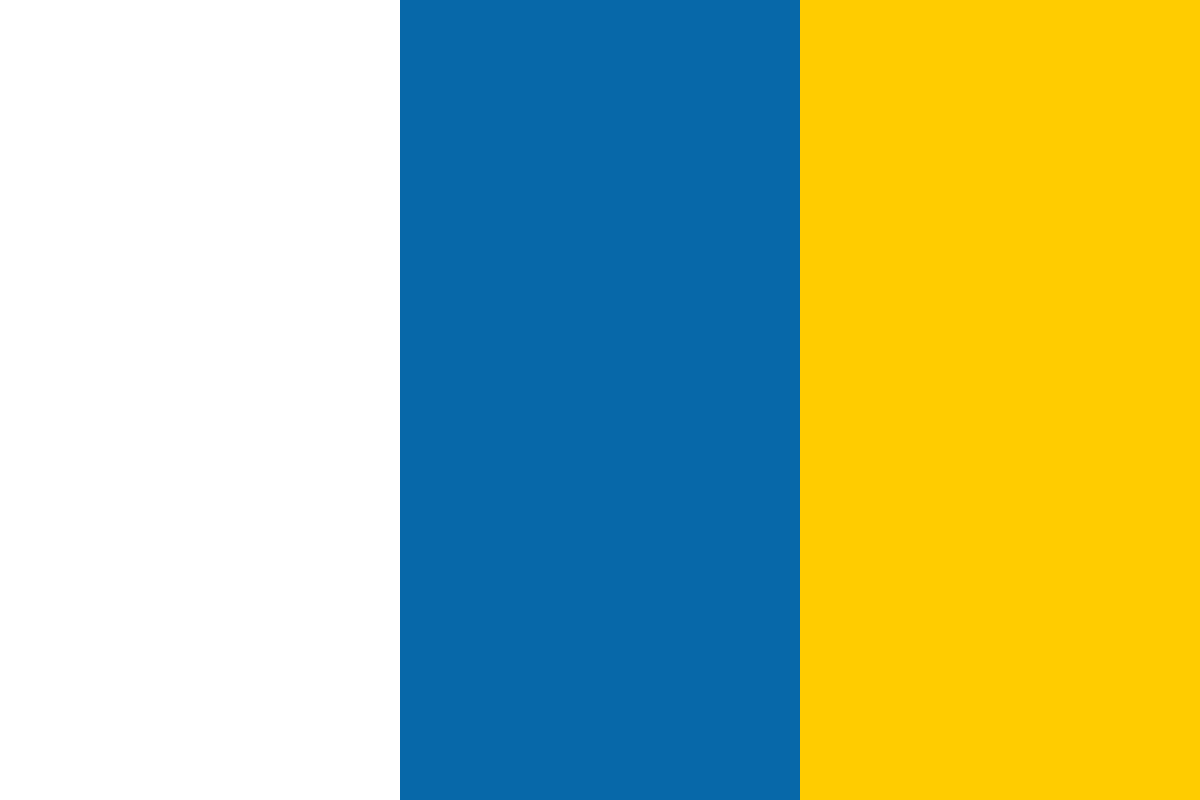

































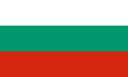








In this article by Ty Audronis, the author of Building Multicopter Video Drone, the process and thought process required to choose a few of the components required to build your multicopter will be discussed.
(For more resources related to this topic, see here.)
Let's dive into the process of choosing components for your multicopter. There are a ton of choices, permutations, and combinations available. In fact, there are so many choices out there that it's highly unlikely that two do it yourself (DIY) multicopters are configured alike.
It's very important to note before we start this article that this is just one example. This is only an example of the thought process involved. This configuration may not be right for your particular needs, but the thought process applies to any multicopter you may build. With all these disclaimers in mind … let's get started!
It sounds obvious, but believe it or not, a lot of people venture into a project like this with one thing in mind: "big!". This is completely the wrong approach to building a multicopter. Big is expensive, big is also less stable, and moreover, when something goes wrong, big causes more damage and is harder to repair. Ask yourself what your purpose is. Is it for photography? Videography? Fun and hobby interest? What will it carry?
There are many configurations, but three of these rotor counts are the most common: four, six, and eight (quad, hexa, and octo-copters). The knee-jerk response of most people is again "big". It's about balancing stability and battery life. Although eight rotors do offer more stability, it also decreases flight time because it increases the strain on batteries. In fact, the number of rotors in relation to flight time is exponential and not linear. Having a big platform is completely useless if the batteries only last two or three minutes.
Once you get into hexacopter and octocopters, there are two basic configurations of the rotors: redundant and independent. In an independent (or flat) configuration, the rotors are arranged in a circular pattern, equidistant from the center of the platform with each rotor (as you go around) turning in an opposite direction from the one before it. These look a lot like a pie with many slices. In a redundant configuration, the number of spars (poles from the center of the platform) is cut in half, and each has a rotor on the top as well as underneath. Usually, all the rotors on the top spin in one direction, and all rotors at the bottom spin in the opposite direction. The following image shows a redundant hexacopter (left) and an independent hexacopter (right):
The advantage of redundancy is apparent. If a rotor should break or fail, the motor underneath it can spin up to keep the craft in the air. However, with less points of lift, stress on the airframe is greater, and stability is not quite as good. If you use the right guidance system, a flat configuration can overcome a failed rotor as well. For this reason (and for battery efficiency), we're going with a flat-six (independent hexacopter) configuration over the redundant, or octocopter configurations.
There is an exorbitant amount of math involved in calculating just how you're going to make your multicopter fly. An entire book can be written on these calculations alone. However, the work has been done for you! There is a calculator available online at eCalc (http://www.ecalc.ch/xcoptercalc.php?ecalc&lang=en) to calculate how well your multicopter will function and for how long, based on the components you choose. The following screenshot shows the eCalc interface:
Although we've decided to go with a flat-six airframe, the exact airframe is yet to be decided. The materials, brand, and price can vary incredibly. Let's take a quick look at some specifications you should consider.
Carbon fiber looks cool, sounds even cooler, but what is it? It's exactly what it sounds like. It's basically a woven fabric of carbon strands encased in an epoxy resin. It's extremely easy to form, very strong, and very light. Carbon fiber is the material they make super cars, racing motorcycles, and yes, aircraft from. However, it's very expensive and can be brittle if it's compromised. It can also be welded using nothing more than a superglue-like substance known as C.A. glue (cyanoacrylate or Superglue).
Aluminum is also light and strong. However, it's bendable and more flexible. It's less expensive, readily available, and can make an effective airframe. It is also used in cars, racing motorcycles, and aircraft. It cannot be welded easily and requires very special equipment to form it and machine it. Also, aluminum can be easier to drill, while drilling carbon fiber can cause cracks and compromise the strength of the airframe.
What we care about in a DIY multicopter is strength, weight, and yes … expense. There is nothing wrong with carbon fiber (in fact, in many ways, it is superior to aluminum), but we're going with an aluminum frame as our starting point.
We'll need a fairly large frame (to keep the large rotors, which we'll probably need, from hitting each other while rotating).
What we really want to look at is all the stress points on the airframe. If you really think about it, the motor mounts, and where each arm attaches to the hub of the airframe are the areas we need to examine carefully. A metal plate is a must for the motor mounts. If a carbon fiber motor mount is used, a metal backplate is a must. Many a multicopter has been lost because of screws popping right through the motor mounts. The following image shows a motor mount (left) where just such a thing happened. The fix (right) is to use a backplate when encountering carbon fiber motor mounts. This distributes the stress to the whole plate (rather than a small point the size of a screwhead). Washers are usually not enough.
Similarly, because we've decided to use an airframe with long arms, leverage must be taken into account on the points where the arms attach to the hub. It's very important to have a sturdy hub that cradles the spars in a way that distributes the stress as much as possible. If a spar is merely sandwiched between two plates with a couple of bolts holding it … that may not be enough to hold the spars firmly. The following image shows a properly cradled spar:
In the preceding image, you'll notice that the spars are cradled so that stress in any direction is distributed across a lot of surface area. Furthermore, you'll notice 45 degree angles in the cradles. As the cradle is tightened down, it cinches the aluminum spar and deforms it along these angles. This also prevents the spars from rolling.
Between this cradling and the aluminum motor mounts (predrilled for many motor types), we're going to use the Turnigy H.A.L. (Heavy Aerial Lift) hexacopter frame. It carries a 775 mm motor span (plenty of room for up to 14-inch rotors) and has a protective cover for our electronics. Best of all, this frame retails for under 70 USD at http://www.hobbyking.com/hobbyking/store/uh_viewitem. asp?idproduct=25698&aff=492101.
Now that we've chosen our airframe, we know it weighs 983 grams (based on the specifications mentioned on the previous link). Let's plug this information into our calculator (refer to the following screenshot). You can see that we've set our copter to 6 rotors, our weight to 983 grams, and specified that this weight is a without Drive system (not including our motors, props, ESCs, or batteries).
You can leave all of the other entries alone. These specify the environment you'd be flying in. Air density can affect the efficiency of your rotors, and temperature can affect your motors. These default settings are at your typical temperature and elevation. Unless you're flying in the desert, high elevations, or in the cold, you can leave these alone. We're after what your typical performance will be.
Let's skip down to the propellers. These will usually dictate what motors you choose, and the motors dictate the ESCs, and the ESCs and motors combined will determine your battery. So, let's take a look at the drive system in that order.
This is another huge point of stress. If you consider it, every bit of weight is supported by the props in the air. So, here it's very important to have strong props that cut the air well, with as little flex as possible, and are very light. Flex can produce bounce, which can actually produce harmonic vibration between the guidance system and the flexing of the props (sending your drone into uncontrolled tumbles).
Does one of the materials that we've already discussed sound strong, light, and very stiff? If you're thinking carbon fiber, you're right on the money. We're going to have a lot of weight here, so we'll go with pretty large props because they'll move a whole lot more air and carbon fiber because they're strong.
The larger the props, the stronger they need to be, and consequently the more powerful the motor, ESC, and battery. Before we start shopping around for parts, let's plug in stats and see what we come up with.
When we look at props, there are two stats we need to look at. These are diameter and pitch. The diameter is simple enough. It's just how big the props are. The pitch is another story. The pitch is how much of pitch the blade has. The tips of a propeller are more flat in relation to the rotation. In other words, they twist. Your typical blade would have something more like a 4.7-inch pitch at 10 inches. Why?
Believe it or not, these motors encounter a ton of resistance. The resistance comes from the wind, and a fully-pitched blade may sound nice, but believe it or not, propulsion is really more of a game of efficiency than raw power. It's all about the balance.
There's no doubt that we'll have to adjust our power system later, so for now let's start big. We'll go with a 14-inch propeller (because it's the biggest that can possibly fit on that frame without the props touching), with a typical (for that size) 8-inch pitch. The following screenshot shows these entries in our calculator:
You can see we've entered 14 for Diameter and 8 for Pitch. Our propellers will be typical two-blade props. Three- and four-blade props can provide more lift, but also have more resistance and consequently will kill our batteries faster. The PConst (or power constraint) indicates how much power is absorbed by the props. The value of 1.3 is a typical value. Each brand and size of prop may be slightly different, and unless the specific prop you choose has those statistics available … leave this alone. A value of 1.0 is a perfectly efficient propeller. This is an unattainable value. The gear ratio is 1:1 because we're using a prop directly attached to a motor. If we were using a gear box, we'd change this value accordingly. Don't hit calculate yet. We don't have enough fields filled out.
It should be said that most likely these propellers will be too large. We'll probably have to go down to a 12- or even 11-inch propeller (or change our pitch) for maximum efficiency. However … this is a good place to start.
In this article, we discussed what are the points to keep in mind when planning to build a multicopter, such as the type of multicopter, number of rotors, and various parameters to consider when choosing the airframe and propellers.
Further resources on this subject: